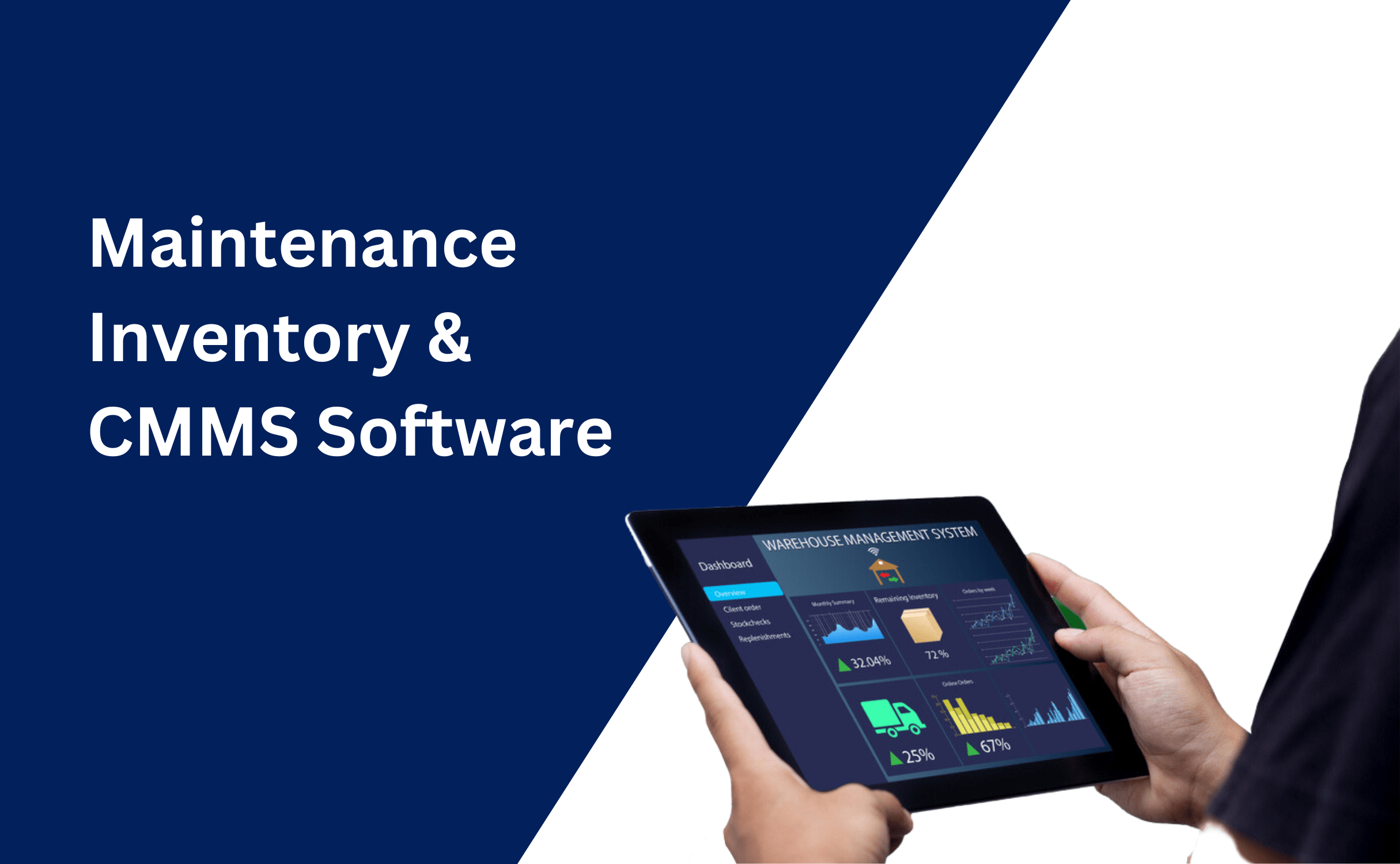
Maintenance Inventory with CMMS Software
In today’s rapidly evolving business environment, efficient operation and maintenance are critical to a company’s overall performance and profitability. Regular maintenance, particularly, plays a significant role in extending the life span of equipment, lowering maintenance costs, reducing unplanned downtime, and improving operational efficiency. This is where Lexicon Tech Solutions comes into play. As seasoned experts, we are committed to providing top-tier device repair and maintenance services across a broad spectrum of enterprises nationwide. Being more than just a service provider, we aim to be our clients’ trusted partners in their journey towards optimal efficiency and profitability.
In the world of maintenance inventory, one tool stands out for its transformative potential: Computerized Maintenance Management Software (CMMS). This powerful software has become a game-changer in maintenance management, offering a plethora of benefits that are critical to the smooth operation of businesses of all sizes.
But what exactly is CMMS, and how can it transform the way businesses handle maintenance inventory?
CMMS or Computerized Maintenance Management Software is a technology platform designed to streamline and automate maintenance management activities. It offers a suite of functionalities, including efficient maintenance scheduling, work order management, real-time tracking of equipment, and maintenance cost analysis. In the context of maintenance inventory, CMMS plays a significant role in managing and controlling the maintenance of spare parts, ensuring that the right part is available at the right time. By leveraging the power of CMMS, businesses can achieve higher operational efficiency, reduce maintenance costs, and improve their bottom line.
Maintenance Inventory and its Challenges
Maintenance inventory, a simple yet crucial concept, refers to the process of managing and controlling the spare parts and materials used for regular and preventive maintenance of equipment. It serves as the backbone of a well-run maintenance department, enabling teams to perform their tasks timely and efficiently. When effectively managed, maintenance inventory can increase equipment reliability, improve team productivity, and significantly reduce maintenance costs.
However, managing maintenance inventory comes with several challenges. Excess inventory, for instance, can tie up substantial financial resources and storage space, whereas lacking the necessary parts at the right time may lead to prolonged downtime.
Furthermore, obsolete inventory – parts that are no longer relevant or appropriate for current equipment – can prove costly and take up valuable space. The unpredictability of unplanned downtime, due to equipment failure or faults, can also result in significant losses.
So, how can businesses address these challenges? This is where the potential of maintenance inventory software shines. Modern inventory management software offers cutting-edge solutions to optimize your inventory level, eliminate obsolete parts, and reduce excess inventory. Such software can also provide real-time insights into your inventory data and automate purchase orders, contributing to improved supply chain efficiency.
As we delve deeper into the world of maintenance inventory management, it’s vital to consider a system that matches your specific needs and helps address these challenges effectively. This brings us to the topic of Computerized Maintenance Management Software, a powerful tool that can revolutionize your maintenance processes.
What to Expect From CMMS Software
Computerized Maintenance Management Software is far more than just a tool; it’s a comprehensive solution that caters to nearly all aspects of maintenance management, from work orders to preventive maintenance and MRO inventory management.
A unique feature that sets CMMS apart from traditional maintenance management methods is its ability to provide real-time tracking. This feature offers businesses real-time insight into their inventory data, including details about each piece of equipment, its maintenance schedule, and the expected lifespan. This information can be accessed using a mobile app, making it simple for you to monitor pertinent details on the go.
Preventive maintenance is another crucial aspect of maintenance management handled by CMMS. Instead of reacting to equipment failures, preventive maintenance enables businesses to anticipate potential problems and deal with them in time. This results in minimized unplanned downtime, thus boosting overall operational efficiency. With CMMS, businesses can schedule preventive maintenance activities, establish a regular maintenance regime, and promptly address any issues that could lead to equipment failure.
One of the cornerstones of effective inventory management is maintaining the right amount of inventory. CMMS proves beneficial here too, serving as a useful tool for MRO inventory management. It helps avoid both overstocking and stockouts through real-time inventory level tracking and a system of alerts for reordering stock.
Moving away from local servers and onto the cloud comes with its own set of benefits. Adopting a cloud-based solution for maintenance inventory management not only cuts down on your IT infrastructure costs but also ensures secure data storage, easy data access, and real-time remote monitoring.
Finally, the adoption of CMMS software can supercharge the efficiency of maintenance teams. By ensuring all relevant information is accessible in just a few clicks, CMMS gives your team the power to respond quickly to maintenance requests, cut down on wasted time, and direct their efforts effectively. This increase in productivity, in turn, translates into noticeable cost and time savings.
In a nutshell, the value that CMMS brings to maintenance inventory is truly transformative, offering businesses a comprehensive approach to tackling the intricacies of maintenance management.
CMMS: A Crucial Tool for Businesses
As we’ve established so far, CMMS is a revolutionary tool, transforming how businesses handle maintenance inventory. But how exactly is it applied in the real world, and what tangible benefits does it offer?
First, let’s discuss operational efficiency. Utilizing CMMS in maintenance inventory management goes a long way in enhancing the overall operational efficiency of an organization. By automating redundant tasks, scheduling preventive maintenance, and generating real-time insights into inventory data, CMMS greatly boosts the productivity of not only the maintenance department but the entire organization.
CMMS also allows for better control over the supply chain and purchase order processing. By tracking the inventory level in real-time, a CMMS solution can alert when it’s time to reorder, ensuring an optimal inventory level at all times and preventing both overstock and stockouts. Further, it can streamline the purchasing process by generating purchase orders automatically, ensuring a smooth supply chain operation.
In regard to maintenance teams, the role of asset management and mobile apps cannot be ignored. Asset management software, an integral part of CMMS solutions, helps in tracking the performance, maintenance schedule, and lifespan of each asset in real time. It offers actionable insights into maintaining assets at their best conditions. Coupling this with the power of mobile apps can further enhance the efficiency of maintenance teams, enabling them to monitor and manage equipment maintenance from anywhere, anytime.
When it comes to reducing maintenance costs, CMMS proves to be an invaluable tool. It supports not just cutting down the direct equipment repair and replacement costs by facilitating regular maintenance but also reducing downtime costs by minimizing unplanned breakdowns.
In conclusion, CMMS solutions present a pathway to effective inventory management. The adoption of such robust software ensures efficient operations, reduces costs, improves supply chain efficiency, and ensures that businesses stay ahead of their maintenance needs, ultimately contributing to their bottom line.
Maintenance inventory plays a pivotal role in preventing downtime and ensuring seamless operations. Lexicon Tech Solutions dedicated services in device repair, and maintenance, and offering refurbished equipment stands as a testament to this. By integrating their solutions, businesses not only extend the life of their equipment but also promote sustainability and cost-effectiveness. In essence, partnering with Lexicon offers a smart, environmentally friendly, and economic avenue to keep businesses running smoothly. Contact our team today!
This blog was reviewed for accuracy by:
Dena Harris, Marketing Director
Dena Harris, the Marketing Director at Lexicon Tech Solutions, is a distinguished marketing expert in the technology sector. With an impressive background in marketing strategies, digital education and over 15+ years in marketing leadership, she possesses a deep understanding of the intricacies of the field. Dena’s keen analytical skills and industry knowledge have served her well at Lexicon Tech Solutions and beyond.