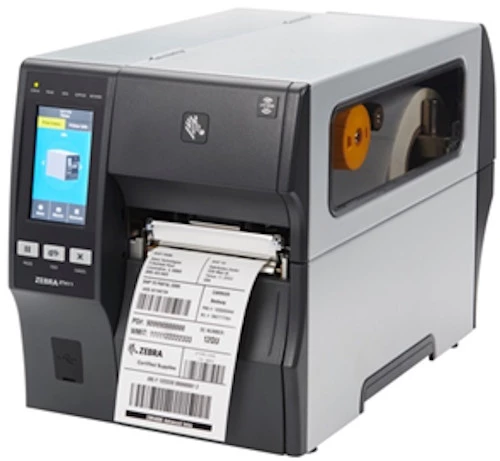
Zebra Printer Troubleshooting: Common Issues & Fixes
If you work in an industry that requires printing labels or barcodes, you’ve probably used a Zebra printer. Zebra printers are known for their reliability and quality, but even the best machines can run into issues from time to time. When your Zebra printer needs to be fixed, it can be frustrating and time-consuming to figure out the problem.
In this blog, we’ll explore some of the most common issues you might encounter with your Zebra printer and provide some troubleshooting tips to help you get back up and running quickly.
Start with General Troubleshooting
Clean the Printer
The first step of troubleshooting a Zebra printer is to clean the entire printer thoroughly. Over time, dust and debris can accumulate on the Printhead, platen roller, and label path, which can cause streaks, smudging, or incomplete printing. To clean your Zebra label printer, follow these instructions provided by Zebra:
Printhead Cleaning Procedure:
- Open the Printhead by moving the Printhead Lever to the OPEN position.
- Remove the media and ribbon (if present).
- Use a cleaning swab (99.7% isopropyl alcohol) and wipe the print elements from end to end. (The print elements are the grayish/ black strip just behind the chrome strip on the underside of the Printhead.) Allow a few seconds for the solvent to evaporate.
- Rotate the Platen Roller and clean thoroughly with a cleaning swab.
- Brush or vacuum any accumulated paper lint and dust away from the Rollers and the Media and Ribbon Sensors.
- Reload ribbon and/ or media, close and latch the Printhead, restore power (if necessary) and run the PAUSE Key self test to check print quality.
Run a Pause Test Print
After you’ve cleaned the printer, run a pause test print. A Pause Test Print is a diagnostic test print that is used to check the print quality and settings of a Zebra printer. When a Pause Test Print is initiated, the printer will pause after printing a few labels, allowing the user to inspect the print quality and make adjustments as necessary. To run a pause test print:
- Press and hold the PAUSE key while turning the printer power ON
- Release the key when the LCD Display says BBlock xxxx
- The PAUSE Key Self Test prints a series of 999 test print labels which can be used for print quality adjustments
- When the printer pauses, press the PAUSE key to restart printing at the same speed. While paused, press the CANCEL key to switch to the next set of labels.
5 Common Zebra Printer Issues
Lexicon Tech has been an industry-leading component-level repair provider for Zebra printers for 25 years. Here are some of the most common issues we fix, potential causes, and how to troubleshoot them.
- Paper jams
- Poor print quality
- Calibration issues
- Connectivity problems
- Ribbon errors
Paper jams
Paper jams can cause costly downtime and wasted resources for those working on the floor. If you’ve run into a paper jam, here’s a few reasons why that could be:
Problem | Potential Cause | Troubleshooting |
Paper jam | Incorrect media loading | Check the media sensor is correctly aligned and not blocked by any debris. Ensure that the media guides are aligned properly to prevent the media from shifting to the side. Make sure that the media roll is loaded correctly, and the label stock is not wrinkled, creased or damaged. Calibrate the printer Make sure the printer settings match the label stock being used, including label size, label orientation, and media type. If all else fails, try resetting the printer to its default settings. |
Dirty or worn out printer rollers | Clean or replace rollers | |
Wrong media type | Check that label media is compatible with the printer model Make sure correct side is facing up and the media guides adjusted to fit the label width Check for any obstructions or debris in the media path Adjust the label sensor position or calibrate the printer for proper media detection | |
Overloading the printer | Print smaller batches Reduce amount of information at once | |
Mechanical issues | Contact a Lexicon Tech Solutions technician for repairs or replacement |
Poor print quality
Poor print quality can impact the accuracy, reliability, and overall performance of the printed parts. Several factors can contribute to poor print quality, including:
Problem | Potential Cause | Troubleshooting |
Poor print quality | Dirty printhead: A dirty printhead can cause uneven heating and result in poor print quality. | Clean the printhead: Use a clean, lint-free cloth and isopropyl alcohol to gently clean the printhead, removing any buildup or debris that may be interfering with print quality. |
Wrong label size or type: Using labels that are not compatible with the printer can result in poor print quality. | ||
Incorrect print speed or darkness settings: If the print speed is too high or the darkness settings are incorrect, the print quality may be affected. | Adjust the darkness setting: Adjust the darkness setting in the printer driver to ensure that the print is neither too light nor too dark. Check the print speed: Slow down the print speed to allow for optimal print quality. | |
Outdated firmware or drivers: Using outdated firmware or drivers can cause compatibility issues and result in poor print quality. | Update to the latest firmware and drivers |
Calibration problems
Calibration issues with Zebra thermal printers can cause a range of problems, including skipping labels, misaligned labels, and poor print quality. Calibration is the process of adjusting the printer’s sensors to recognize the gap between the labels and adjust the printing accordingly. If the printer is not properly calibrated, it may not be able to detect the gap between labels or it may print incorrectly.
Problem | Potential Cause | Troubleshooting |
Misaligned labels | Label sensor is not calibrated correctly Label format is not set up properly | Perform label sensor calibration, check label format settings, and adjust the label guide position. |
Skipping labels | Incorrect label calibration Dirty sensors Worn out platen rollers Software issue (incorrect label formatting or a mismatch between the printer driver and label design software.) | Make sure the printer is properly calibrated for the label size and type being used. Check the sensors and platen rollers for dirt or damage, and clean or replace them as necessary. If the issue persists, try adjusting the label formatting or double-checking that the correct printer driver and label design software are being used. Test the printer with a different label roll to determine if the issue is with the printer or the labels themselves. |
Skewed label printing | The label stock is not loaded correctly Print head pressure is not set properly | Adjust the label guide and label stop position, and ensure that the print head pressure is set correctly. |
Connection Issues
Connection problems are a top issue for 3D printers because they can lead to failed prints and wasted time and resources. There are several ways in which connection problems can occur:
Problem | Potential Cause | Troubleshooting |
Printer not responding to print requests | Outdated or wrong printer drivers Network connection issue Printer is not set as the default printer Printer is offline or disconnected | Download and install the latest printer drivers from the Zebra website Check the network connection and make sure the printer is connected to the correct network Set the printer as the default printer in the computer settings Check the printer status |
The printer goes offline or disconnects frequently | Network settings need to be adjusted Outdated firmware or drivers Printer is set to “sleep mode” or power-saving mode | Adjust network settings to ensure the printer has a stable connection Update the printer firmware and drivers to the latest version Adjust power settings to prevent the printer from going to sleep mode or power-saving mode. |
Slow printing speed | Network congestion Print resolution is too high Outdated firmware or drivers Insufficient memory or processing power | Check the network bandwidth and reduce other network activities to improve the printing speed Adjust the print resolution to a lower setting Update the printer firmware and drivers to the latest version Upgrade the printer memory or processing power if possible. |
Error messages indicating a communication error | Network connection issues Printer drivers need to be updated or reinstalled Printer firmware needs to be updated Incorrect printer settings | Check the network connection and make sure the printer is connected to the correct network Update or reinstall the printer drivers Update the printer firmware to the latest version Check the printer settings and ensure they are configured correctly. |
Ribbon issues
Ribbons transfer ink to the label so issues can lead to costly downtime and reprints, making it crucial to maintain and troubleshoot any ribbon-related problems.
Problem | Potential Cause | Troubleshooting |
Ribbon wrinkling | Ribbon too loose or tight Wrong tension settings Worn out ribbon guides | Check tension Check ribbon spool Check printhead Check ribbon type Check label material Adjust printer settings |
Ribbon breakage | Tension on the ribbon is too tight or too loose. The printhead pressure is too high. The ribbon is not threaded correctly. The ribbon is defective or expired. The wrong ribbon type is being used for the label material. | Adjust ribbon tension: Check the printer manual for instructions on adjusting the tension on the ribbon. Make small adjustments until the ribbon feeds smoothly without breaking. Adjust printhead pressure: Check the printer manual for instructions on adjusting the printhead pressure. Make small adjustments until the ribbon feeds smoothly without breaking. Thread the ribbon correctly: Check the printer manual for instructions on how to thread the ribbon correctly. Make sure the ribbon is loaded properly and not twisted or folded over. Replace the ribbon: If the ribbon is defective or expired, replace it with a new one. Use the correct ribbon type: Make sure the ribbon type matches the label material being used. If unsure, consult the printer manual or contact the ribbon manufacturer for guidance. |
Third-Party Maintenance with Lexicon Tech
Lexicon Tech offers reliable third-party maintenance and repairs for hardware components. We order bulk hardware replacement parts and store them in our warehouse, allowing us to provide timely repairs or replacements when needed. Our maintenance contract can help ensure that your business or organization is able to run smoothly with minimal disruptions.
Contact Lexicon to learn more about our service contracts for hardware equipment.