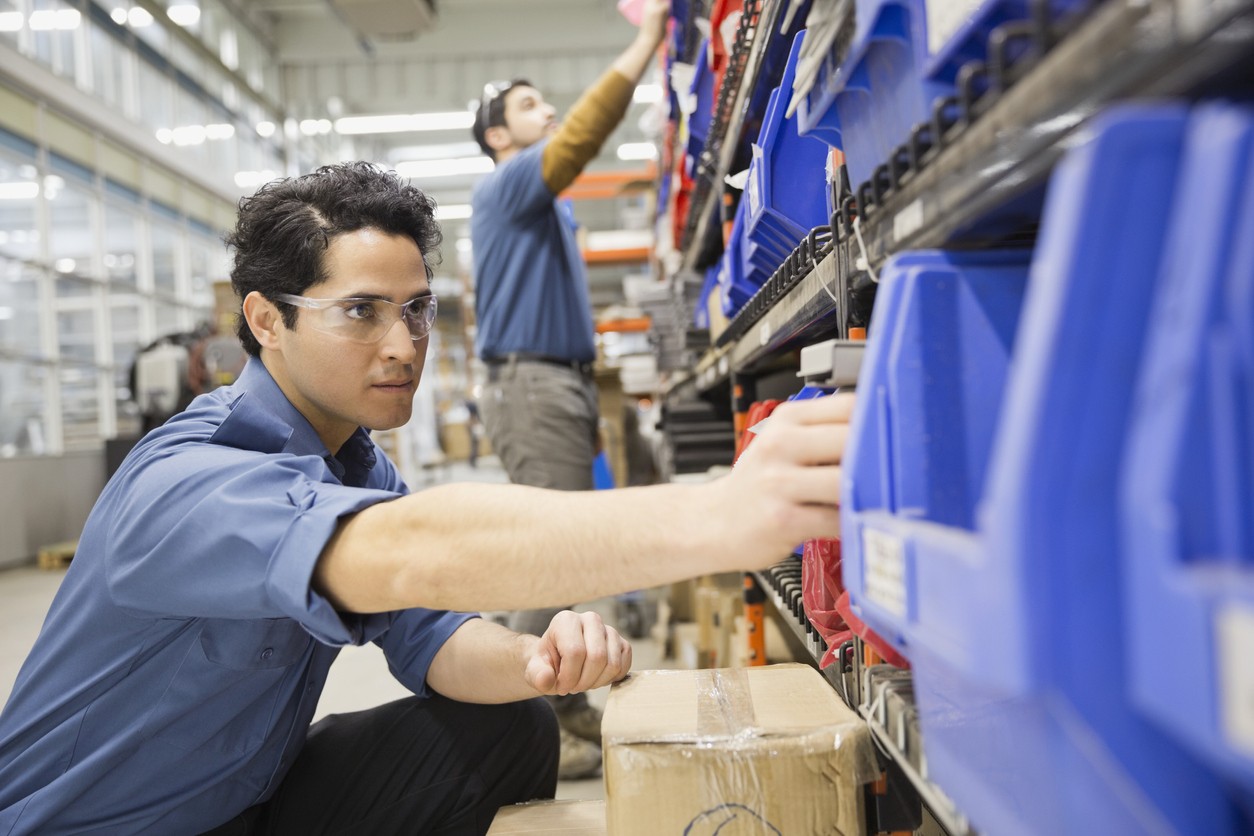
Improving Efficiency and Customer Satisfaction with Your Order Picking Strategy
Warehouse order picking is a fundamental component of the supply chain, playing an impactful role in determining success or failure in warehouse operations. Order picking is the method of pulling items from inventory to fulfill a specific customer order, which makes it a decisive factor in customer satisfaction. As most labor costs in warehouse operations go towards order picking, it is essential to ascertain that it is performed as efficiently, accurately, and effectively as possible.
Within the broader concept of warehouse order picking, four principal methods stand out: batch picking, wave picking, discrete picking, and zone picking. Each picking method caters to different needs, making it vitally important to understand them all.
- Batch picking involves the process of picking multiple customer orders simultaneously, thereby reducing travel time within the warehouse.
- Wave picking organizes orders in waves based on shipping appointments or other critical factors.
- Discrete picking strategies are essentially single-order picking techniques, focusing on one order at a time to ensure high-order accuracy.
- Zone picking assigns warehouse workers to specific areas or zones in the warehouse, with each picker being responsible for picking some or all items from their zone.
Deciding which method is best can significantly impact the efficiency of warehouse operations and, consequently, affect customer satisfaction. A fundamental understanding of the unique attributes of each method is vital to selection. Regardless of the method chosen, warehouse order picking guarantees a smoother supply chain and a more compelling shopping experience for the customer.
Order Picking Processes and Their Vital Role in Customer Satisfaction
The foundation of every flourishing distribution center lies in drafting and executing an expertly streamlined order picking process. Accurate order picking goes beyond just handling inventory effectively; it determines customer satisfaction by ensuring orders are fulfilled correctly and in a timely manner.
In the order picking process, after a customer order is received, the warehouse worker, often referred to as the order picker, uses their designated picking method such as batch picking, wave picking, discrete picking, or zone picking to locate the agreed items in the warehouse and subsequently gathers them for shipping. A properly organized warehouse layout can significantly enhance this process, enabling pickers to swiftly find and collect the required products.
What customers value the most, apart from the quality and price of the products, is receiving the right order punctually. In essence, the functionality of the order-picking process is reflected in customer satisfaction. A mishap at any stage of the order-picking process, such as poor picker performance or incorrect item selection, can lead to a domino effect that harms customer satisfaction.
The role of an efficient order picker in such an environment can’t be overstated. A talented picker will not only know the order picking process like the back of their hand but will also be capable of avoiding common pitfalls. The skills and experience of an order picker can significantly influence the operational success of a distribution center.
A proficient order picker understands that every inaccurate order not only costs money to correct but can also potentially cost the company a valuable customer. Therefore, the merging of a streamlined order picking process with skillful order pickers can promote customer satisfaction to new heights.
Involving Modern Technology in Your Warehouse Operations
Warehouse operations and order picking, in particular, have experienced groundbreaking transformations with the advent of modern technology. This adoption drives order accuracy and has turned several tedious manual tasks into automated processes, thereby boosting efficiency and productivity.
One of the pivotal technologies being adopted in order fulfillment is the use of barcode scanners. Barcode scanners have a significant role in making the picking process faster, more accurate, and less prone to human error. By introducing barcode scanners, warehouse managers can ensure that pickers choose the correct items, verify the picked items against the customer order, and update warehouse inventory in real time.
Artificial Intelligence (AI) has also begun to make strides in warehouse operations, offering promising future developments. AI can model and simulate warehouse operations, providing valuable insights that lead to optimized warehouse efficiency. Additionally, AI-backed systems ensure high order accuracy by cross-verifying order data, keeping track of inventory changes, and identifying potential mistakes in the picking process.
A well-integrated Warehouse Management System (WMS) is another valuable tool in modern warehouse operations. It meticulously controls and manages the operational aspects of the warehouse, including inventory management, the picking process, and order fulfillment. A competent WMS enables warehouse managers to monitor daily operations, measure performance, and make informed decisions, fostering a more effective picking process.
These tech advancements, combined appropriately, offer a layered approach to improving order picking methods. They can drastically reduce errors, expedite the picking process, and retain a high level of accuracy, all of which reflect positively on customer satisfaction.
Which Order Picking Strategy is Right For Your Organization’s Efficiency?
Travel time can often be a warehouse’s largest operational cost, especially in larger facilities. Minimizing the picker’s travel time reduces costs and increases productivity. Employing different methods like wave, batch, or zone picking, re-arranging the warehouse layout to reduce travel distance, and implementing a Warehouse Management System (WMS) could be viable solutions.
The decision between picking a single order or using multi-batch picking can greatly affect efficiency and cost. Single-order picking demands the picker to handle one order at a time, whereas multi-batch picking involves gathering items for several customer orders together. The choice between the two largely depends on the warehouse’s size, the type, and quantity of orders to fulfill, as well as the manpower and technologies available. However, generally, multi-batch picking tends to be more efficient in larger operations, reducing travel time and boosting picking speed.
A comprehensive picking strategy is equally significant for warehouses of all sizes. This includes exploring different methods like zone picking, where pickers are assigned to specific areas; voice picking, an AI-powered system where pickers receive voice commands for tasks; or cluster picking, which involves picking several orders simultaneously from the same zone. These strategies can lower labor costs, boost efficiency, and improve customer satisfaction by reducing errors and speeding up the order fulfillment process.
Lexicon Tech Solutions: Your Partner in Achieving Warehouse Efficiency
Lexicon Tech Solutions is a market-leading Georgia-based company that provides third-party maintenance, repair, and refurbished equipment for printers, barcode scanners, and mobile computers. We specialize in large-scale technology maintenance for different bodies, from schools to businesses, to resellers and OEMs.
We understand the importance of high-performance barcode scanners in the warehouse order picking process. As part of our preeminent service catalog, our range of barcode scanners is designed to enhance order-picking efficiency, order accuracy, and ultimately, customer satisfaction. Our barcode scanners reduce manual handling, speed up the picking process, and are an indispensable tool for reducing labor costs.
Additionally, our refurbished equipment is ergonomic, resilient, and feature-rich, which ensures pickers are well-equipped to handle complex warehouse operations. Coupled with our top-notch service and maintenance, we provide technology solutions that are aligned not only with your immediate needs but also with your long-term business goals.
Incorporating our tech solutions with the strategies discussed earlier—optimizing warehouse layout to reduce travel time, choosing the correct order picking method, and advancing rightfully integrated technologies in operations—will boost order picking efficiency and uplift overall warehouse productivity.
Embrace the future of warehouse operations with Lexicon Tech Solutions where technology meets expertise and quality is paramount. Reach out to us today, and let’s discuss how we can help maintain and repair your technology fleet.