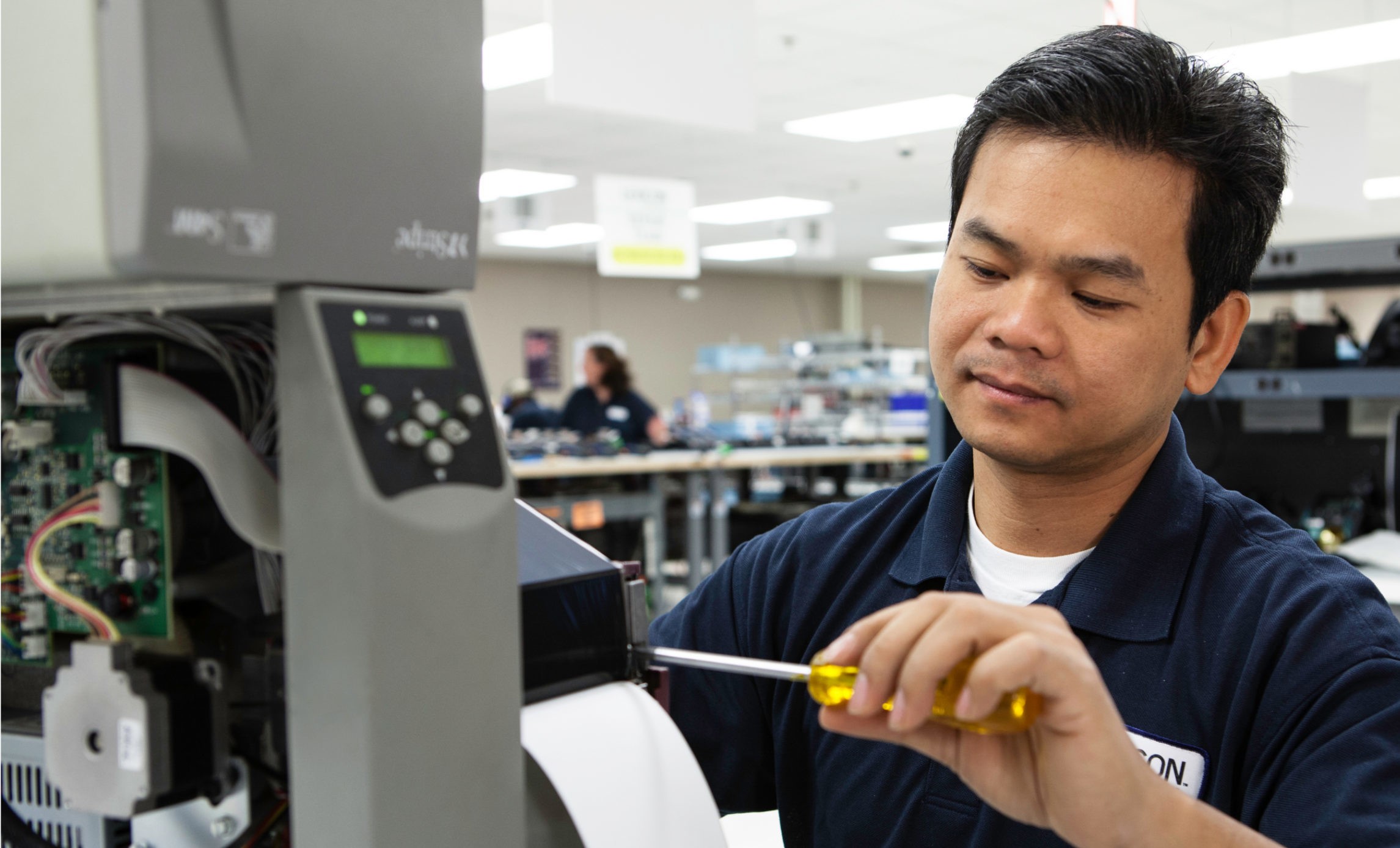
Happenings from Lexicon’s RepairFactory
Scaled at 50,000 square feet and growing, RepairFactory combines the power of industry-certified processes, the capabilities of state-of-the-art equipment and expertise of highly-trained technicians.

Lexicon knows our way around a motherboard. Our X-ray and BGA rework capabilities ensure devices are repaired at the component level.
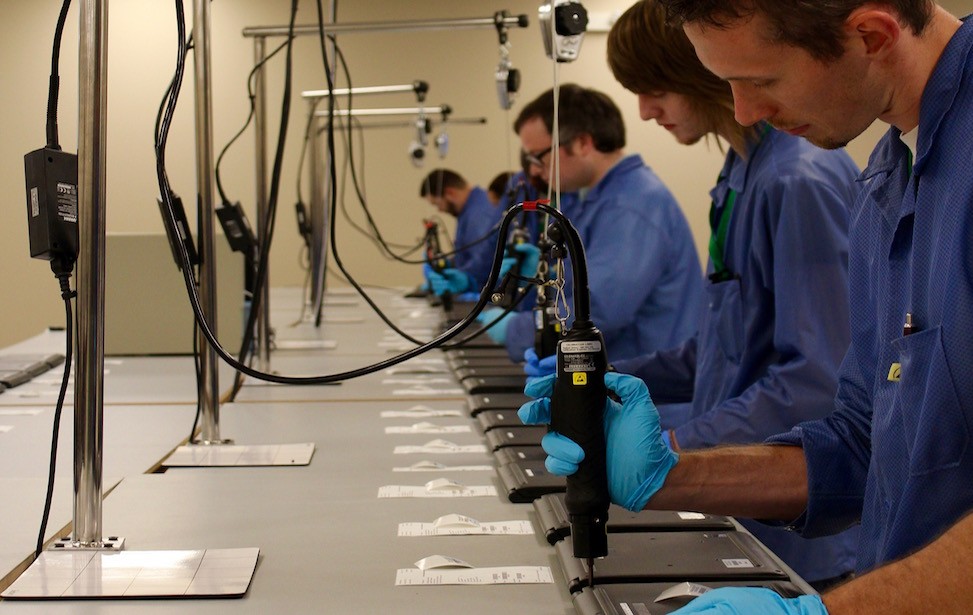
It’s built for speed and agility, with 1000 RPMs of power and pivotal response — it’s not the latest Tesla, it’s RepairFactory’s Torque Arm Station, built to cut time and optimize efficiency.
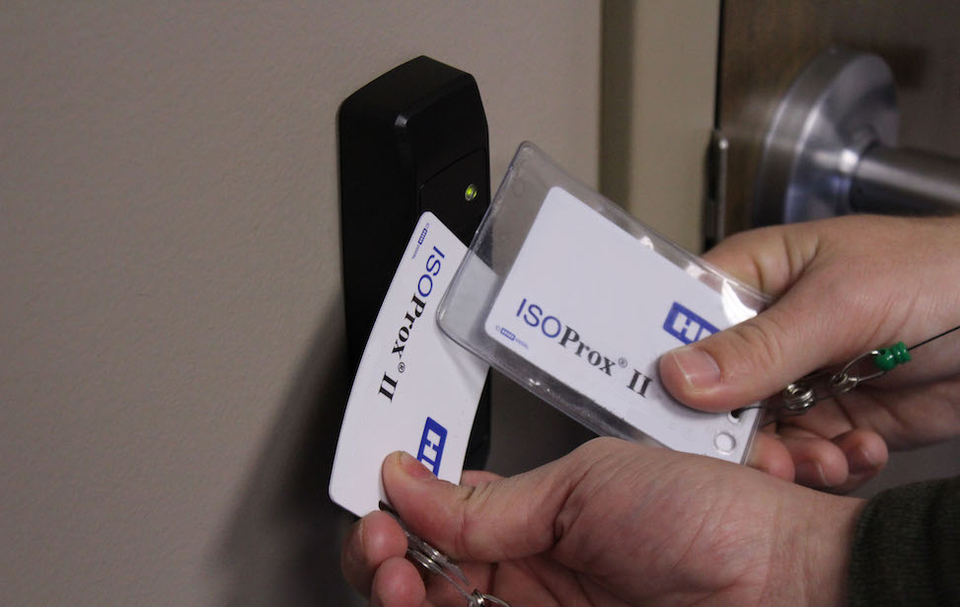
Layers of security for PCI encryption make the “Get Smart” entry look simple — dual redundancy ensures no one person has access to perform a single step alone in the key injection process.
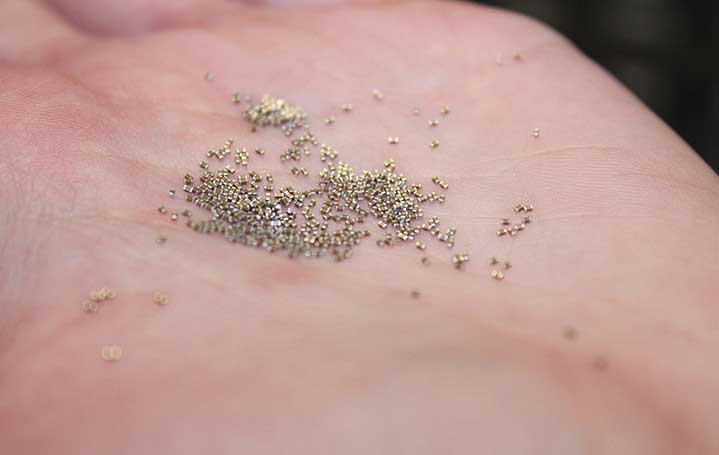
This isn’t pixie dust, but it does represent a little bit of magic that happens every day at Repair Factory. Lexicon repairs microchips two sizes smaller than these.
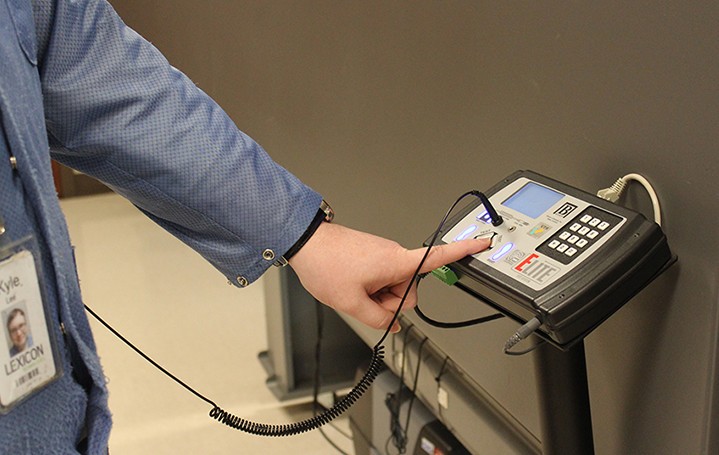
While James Bond might enter work with an iris scan, Lexicon teams measure their electrostatic discharge levels before passing onto the repair floor.
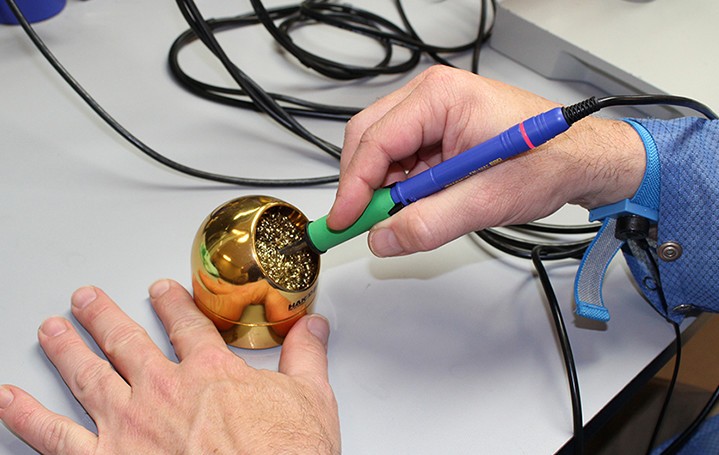
There really is a pot of gold at the end of the rainbow. Repair tools stay precise with constant cleaning and care from Lexicon Technicians.
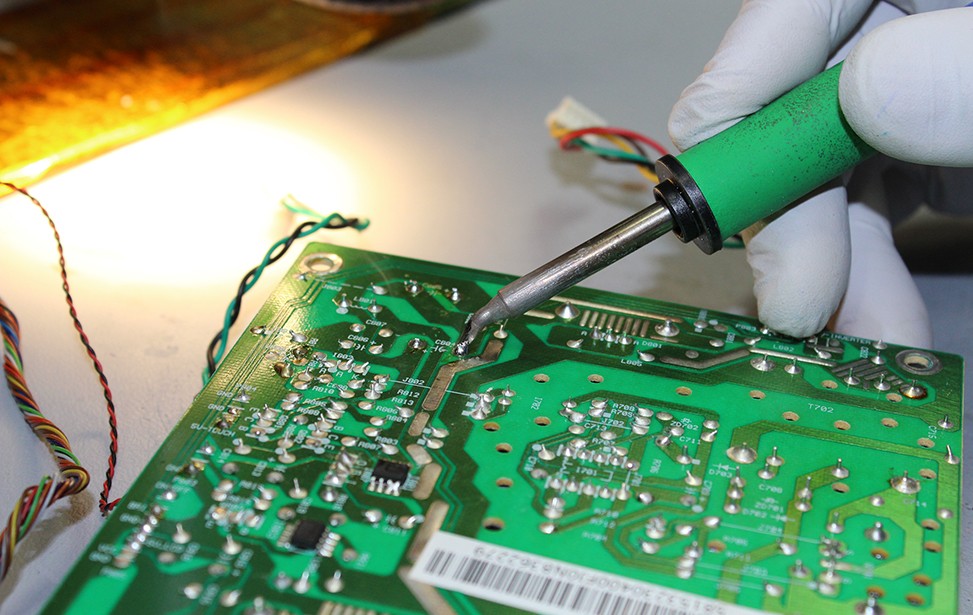
Things are heating up on the Repair Floor. Specially trained technicians use soldering techniques to perform component-level repair.
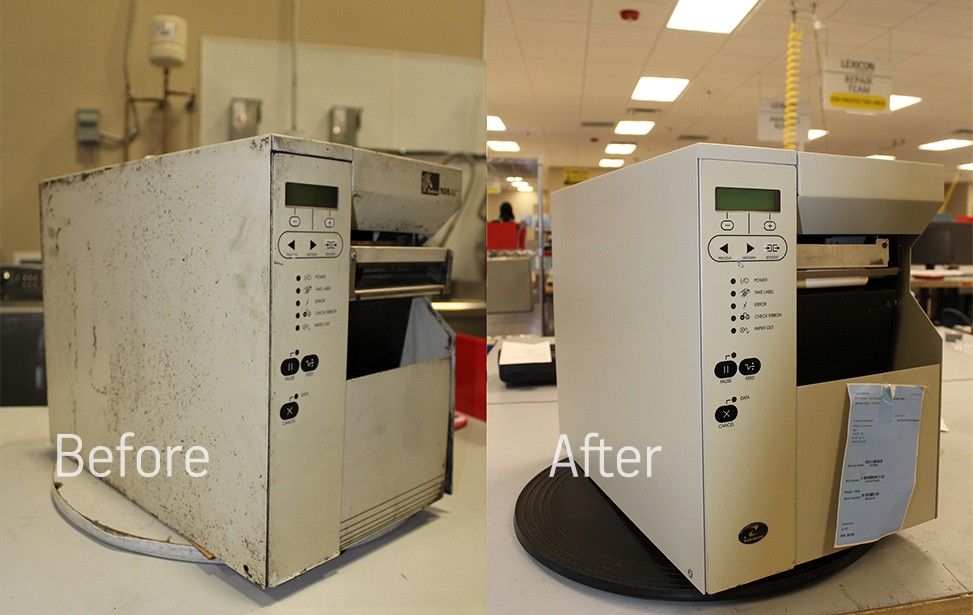
Pressure wash, a bit of fine tuning and a new paint job. Lexicon-Certified refurbished techniques drive label printers to like-new status.
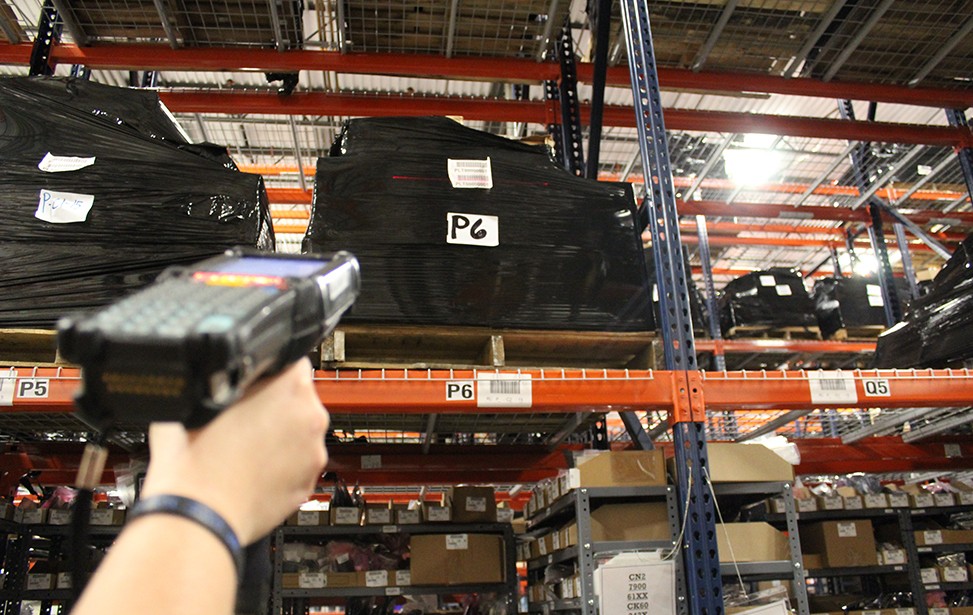
It’s quick like lightning! This little laser gives our logistics team the power to view the contents of an entire pallet with one quick point-and-shoot scan. (Thanks to our friends at Foxfire.)
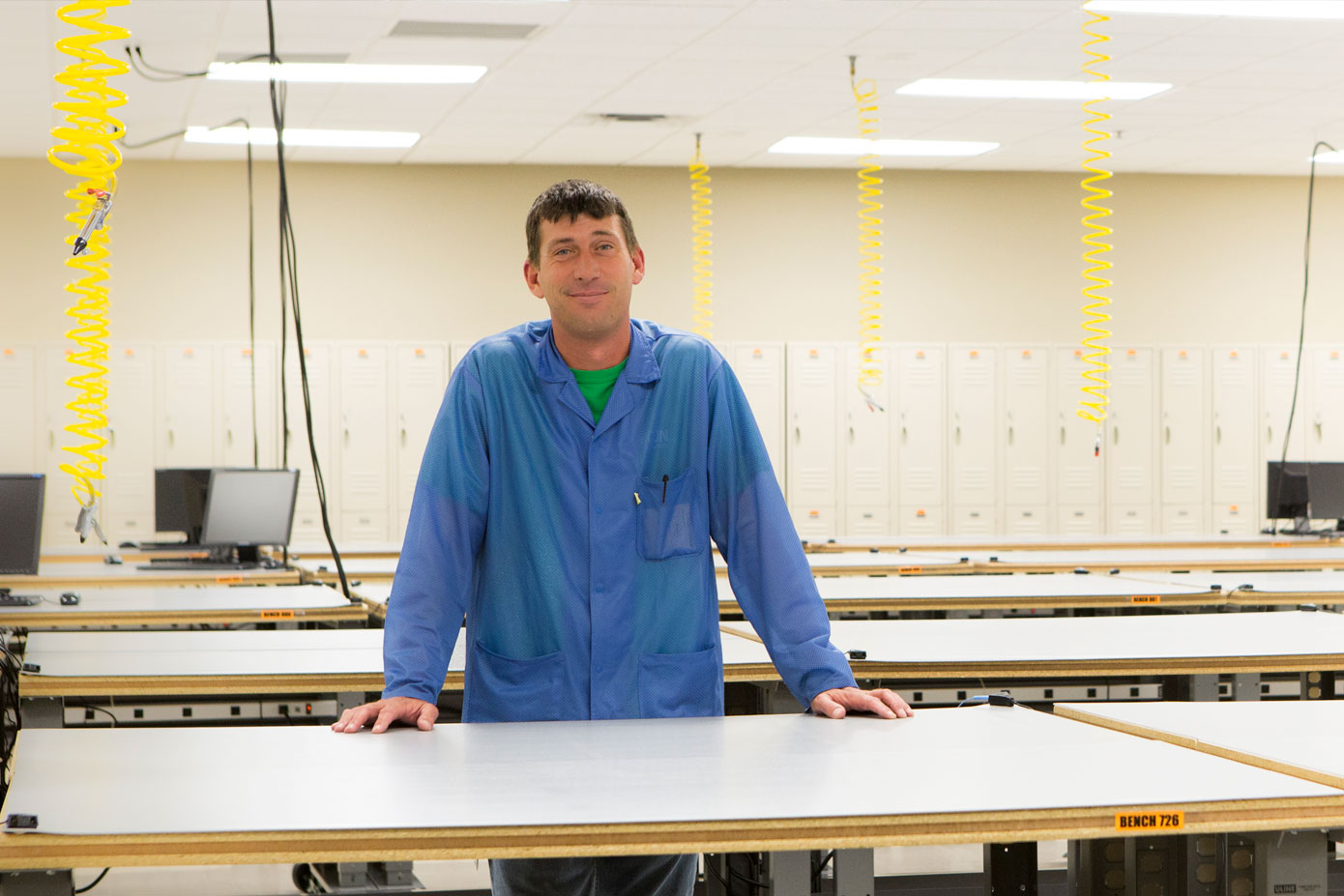