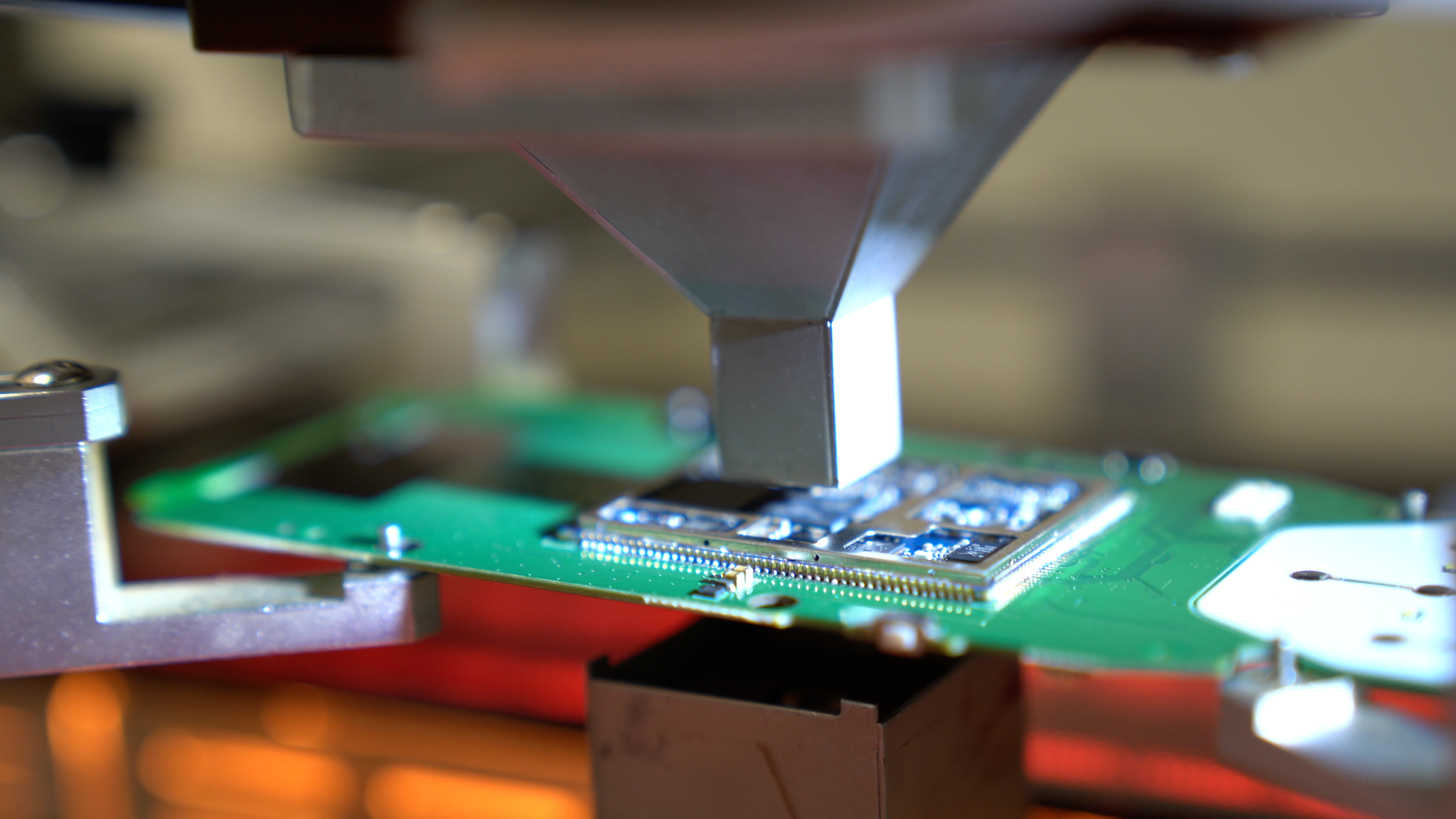
Predictive Maintenance vs Preventive Maintenance: What’s the Difference?
Imagine you’re managing a bustling warehouse, reliant on a fleet of mobile computers and printers to efficiently process inventory and orders. Suddenly, one critical mobile device fails without warning, bringing the entire operation to a standstill. Your productivity plunges, customers grow impatient, and profits take a hit.
This is an unfortunate reality for many companies that overlook maintaining their equipment. To avoid such detrimental situations, you need a robust maintenance strategy to keep operations running smoothly.
Let’s explore two crucial maintenance strategies that can ensure seamless operations for your equipment – predictive maintenance and preventive maintenance. Predictive maintenance focuses on anticipating and addressing potential issues based on real-time data, while preventive maintenance involves scheduled routine maintenance tasks to prevent failures before they occur.
What is Preventive Maintenance?
Preventive maintenance for barcode scanners, printers, and mobile computers involves a proactive approach to ensure optimal performance, extend device lifespan, and minimize potential downtime. A preventive maintenance schedule can help identify and address potential issues before they escalate into significant problems.
Here are the key components of preventive maintenance for barcode scanners and mobile computers:
- Regular Inspections: Conduct scheduled inspections of the barcode scanners, printers, and mobile computers to check for physical damage, loose connections, and signs of wear. Regular inspections help identify any potential issues early on and allow for timely repairs or replacements.
- Cleaning and Calibration: Barcode scanners and mobile computers used in shipping and fulfillment environments are exposed to various elements that can affect performance, such as dust, dirt, and humidity. Cleaning the devices regularly, including the scanner lens and touchscreens, ensures accurate barcode reading and smooth functionality. Calibrating the devices optimizes touch sensitivity and display accuracy.
- Battery Maintenance: Preventive maintenance includes monitoring battery health, optimizing battery charging practices, and replacing batteries when necessary to avoid unexpected power failures.
- Software Updates: Regularly update the firmware and software on the barcode scanners and mobile computers to ensure they have the latest features, security patches, and bug fixes. Keeping the devices up-to-date enhances their performance and protects them from potential security vulnerabilities.
- Testing and Performance Verification: Conduct periodic performance tests to verify that the barcode scanners and mobile computers are functioning as expected. Testing should cover barcode scanning accuracy, wireless connectivity, and overall system performance.
- Replacement of Consumables: Barcode scanners, especially those integrated into mobile computers, use consumables such as labels and ribbons. As part of preventive maintenance, replace these consumables when needed to maintain optimal print quality and readability.
- Environmental Considerations: Shipping and fulfillment environments can be challenging, with exposure to varying temperatures, humidity levels, and potential physical hazards. Implement measures to protect the devices from harsh conditions and consider using protective cases or sleeves when necessary.
- Training and User Support: Ensure that users are well-trained in handling and operating the barcode scanners and mobile computers properly. User knowledge and adherence to best practices can prevent accidental damage and improve overall device longevity.
- Documentation and Record Keeping: Maintain detailed records of all maintenance activities, including inspection results, repairs, and component replacements. Keeping accurate records helps track the devices’ health over time and assists in making data-driven decisions for future maintenance needs.
What is Predictive Maintenance?
Predictive maintenance takes a data-driven and proactive approach to monitor device health and predict potential failures before they occur. By leveraging real-time data, advanced analytics, and machine learning algorithms, businesses can stay ahead of performance issues, minimize downtime, and optimize the maintenance process.
Here are the key components of predictive maintenance:
- Condition Monitoring Sensors: Sensors continuously collect data on various parameters such as temperature, battery health, device usage, and other critical performance metrics.
- Data Collection and Storage: Centralized data collection and storage system gather real-time data generated by the condition monitoring sensors. Cloud-based solutions are commonly used to store and manage large volumes of data efficiently.
- Data Analysis and Pattern Recognition: Algorithms can recognize patterns, trends, and anomalies in the data to identify potential signs of equipment degradation or impending failures.
- Predictive Algorithms: Develop predictive algorithms that utilize historical data and real-time inputs to predict the remaining useful life of the barcode scanners and mobile computers. These algorithms consider factors such as device usage patterns, environmental conditions, and previous maintenance history.
- Early Warning Systems: Implement early warning systems that trigger alerts or notifications when the predictive algorithms detect potential issues. These alerts enable maintenance teams to take immediate action before the problems escalate into major failures.
- Proactive Maintenance Scheduling: Based on the predictions and insights provided by the predictive algorithms, schedule maintenance activities at the most opportune times. This ensures that maintenance is performed when it is most effective and least disruptive to operations.
- Reduced Downtime and Improved Efficiency: By predicting potential failures in advance, businesses can take preventive measures and replace components proactively. This reduces unexpected downtime and ensures that the barcode scanners and mobile computers operate at their peak efficiency.
- Continuous Monitoring and Iterative Improvement: Predictive maintenance is an ongoing process that involves continuous monitoring and analysis. As more data is collected and analyzed, the predictive algorithms can be refined to improve accuracy and provide even more reliable predictions.
- Integration with Asset Management Systems: Integrate the predictive maintenance system with existing asset management systems to streamline maintenance workflows and ensure seamless coordination between predictive maintenance tasks and other maintenance activities.
The Main Differences Between Predictive and Preventive Maintenance
While both aim to optimize asset performance and minimize costs, there are several key differences between these two maintenance strategies. Understanding these differences can help businesses make informed decisions about the most suitable approach for their maintenance needs.
Aspect | Predictive Maintenance | Preventive Maintenance |
Goal | Timely intervention to prevent equipment failure. | Prevent potential issues from arising and maintain equipment in optimal condition. |
Timing | Relies on real-time data and immediate decision-making. | Operates on regular intervals predetermined by maintenance schedules. |
Data Analysis | Uses real-time data and advanced analytics (AI, ML). | Relies on historical data analysis and asset condition monitoring. |
Types of Maintenance Tasks | Addresses critical assets and specific failures. | Covers routine maintenance tasks and general equipment checks. This includes inspections, lubrication, calibration, and other preventive measures to maintain equipment reliability and performance. |
Selecting the Right Maintenance Strategy for Your Organization
Factors to Consider in Maintenance Strategy Selection
Choosing the appropriate maintenance strategy for your organization depends on several factors that should be taken into consideration:
- Asset Criticality: Assess the importance of devices to your organization’s operations. High criticality assets may require a more advanced maintenance strategy, such as a predictive maintenance program, while lower criticality assets can be effectively managed with preventive maintenance.
- Process Requirements: Consider the specific requirements of your processes. Some processes may demand high reliability and minimal downtime, making predictive maintenance the preferred choice. Others may tolerate a certain level of downtime and can be adequately maintained through preventive maintenance practices.
- Budget Constraints: Evaluate your organization’s budget limitations. Predictive maintenance often requires significant investment in condition monitoring equipment and skilled personnel, while preventive maintenance is generally more cost-effective and can be implemented with fewer resources.
The Power of Combined Maintenance Approaches
A comprehensive maintenance approach often involves combining predictive and preventive maintenance strategies to leverage their respective benefits:
- Predictive Maintenance: With its proactive nature, predictive maintenance helps identify potential issues in advance through continuous monitoring and analysis of asset conditions. It minimizes unplanned downtime and reduces the risk of equipment failure.
- Preventive Maintenance: By regularly performing scheduled maintenance tasks, preventive maintenance aims to prevent asset failures and maximize equipment reliability. It reduces the likelihood of unexpected breakdowns and extends the lifespan of assets.
By integrating predictive and preventive maintenance, organizations can achieve a balanced approach that optimizes asset performance, minimizes downtime, and reduces costs. Predictive maintenance identifies potential problems, allowing for targeted maintenance actions, while preventive maintenance ensures routine maintenance tasks are performed to prevent failures.
Customized Preventive Maintenance Program with Lexicon Tech Solutions
Streamline your device maintenance across a multitude of technology models from all leading manufacturers. Our cloud-based technology maintenance platform, RepairEngine, manages scheduling, service level performance, spare devices, technician assignment, and tracking for maintenance events across all manufacturer types and models throughout your organization.
Ready to experience the benefits of preventive maintenance with Lexicon Tech Solutions? Contact us today to learn more about how we can customize a maintenance plan that suits your unique needs.