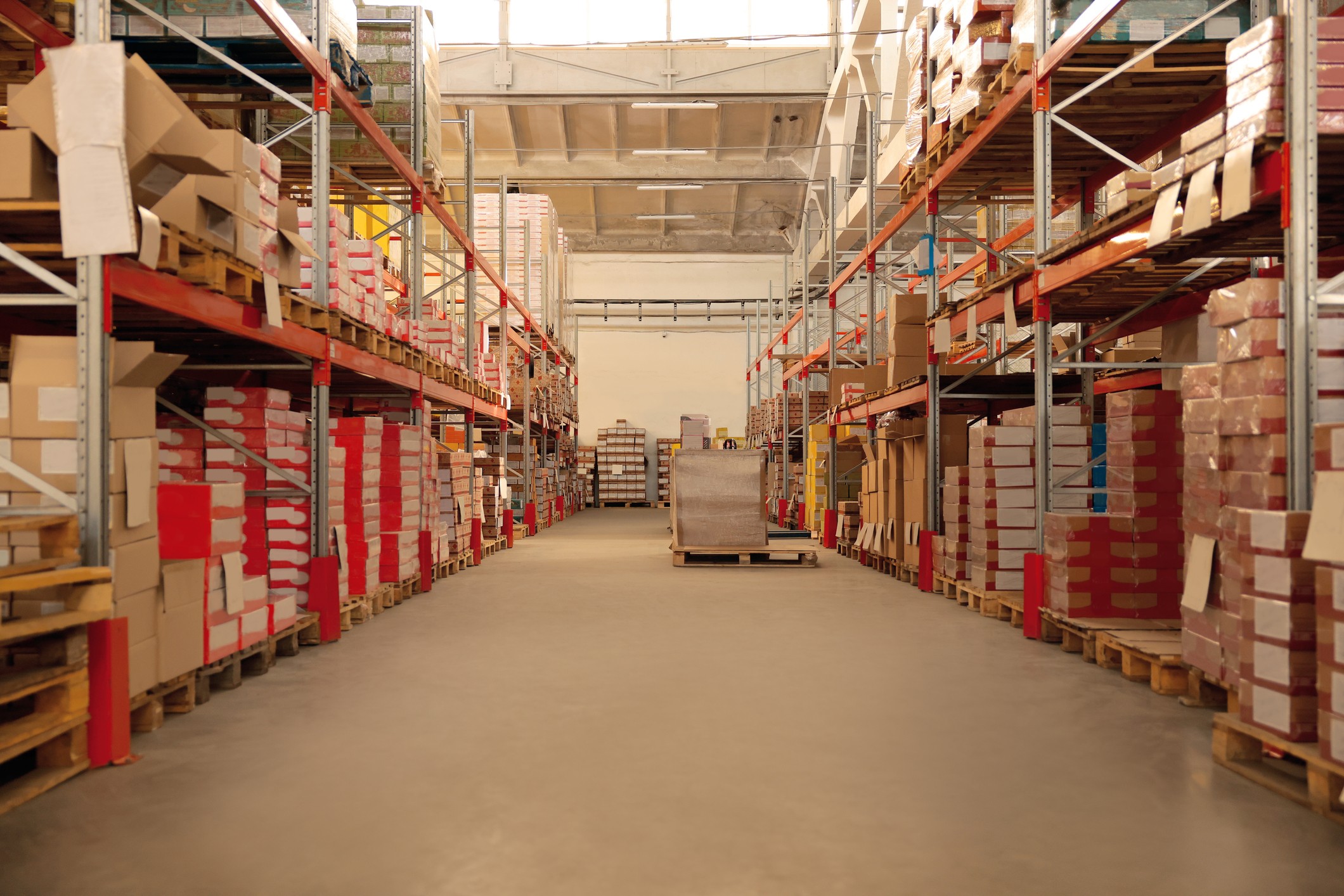
What is Case Picking? How to Optimize for Your Warehouse
Efficient warehouse operations are vital for success, and a core component of these operations is case picking, a process at the heart of distribution centers where large quantities of individual items reside. This function ensures products are swiftly picked, packed, and dispatched to their destinations.
At Lexicon Tech Solutions, our extensive experience in technology repair and support offers unique insights into warehouse operations. We’re here to navigate you through case picking and explore how you can optimize the process to boost the efficiency of your warehouse.
What is Case Picking?
Case picking is a warehouse operation that involves selecting full cases or carton quantities of products from storage locations to fulfill customer orders. This process is typically used when customers place orders for larger quantities of products or when the products are packaged in cases rather than individual items.
This differs from other picking methods such as piece picking, where individual items are selected, or batch picking, where multiple orders are picked simultaneously.
Pros and Cons of Case Picking
Case picking is a popular method for warehouses that handle high-volume orders. It allows for faster and more efficient fulfillment, reducing the time required to gather multiple individual items for each order. With case picking, the picking process becomes more streamlined, leading to improved order accuracy and faster order fulfillment.
Compared to other picking methods, case picking offers several advantages.
- It reduces the number of individual picks required, resulting in less travel time and increased productivity.
- It simplifies the packing process, as full cases can be easily organized and loaded onto shipping containers.
- Case picking allows for efficient storage and retrieval of products with higher demand or products that are frequently ordered together.
However, it’s important to consider the potential drawbacks of full case picking as well.
- It requires dedicated storage space for full cases, which may limit storage density.
- Maintaining an optimal inventory balance and rotation can be challenging in warehouses with a diverse range of products as full cases may need to be broken down and repackaged at times.
How to Optimize Case-Picking Operations
To achieve maximum efficiency in your case picking operations, it’s crucial to optimize various aspects of your warehouse. Let’s explore some key strategies to enhance the efficiency of case picking:
Storage System Considerations:
A well-designed and organized storage system is essential for efficient case picking. Consider implementing systems like carton flow or pallet flow, which use gravity to ensure products move forward, maintaining proper rotation and accessibility. This eliminates the need for excessive manual handling and reduces travel time between picking locations. Optimizing your storage system can significantly improve the speed and accuracy of case picking.
Implementing Technology Solutions:
Warehouse automation technologies can greatly enhance case-picking efficiency. One example is a retrieval system that utilizes automated equipment such as autonomous mobile robots (AMRs) or pallet jacks. These advanced systems can quickly retrieve full cases from storage locations, eliminating the need for manual picking and reducing labor costs. Additionally, barcode scanners can enhance accuracy by ensuring correct item selection and proper tracking throughout the picking process.
Reducing Labor Costs:
Automated systems and technologies decrease reliance on manual labor for picking operations. This reduces labor expenses and minimizes the potential for errors. Investing in staff training, implementing efficient workflow processes, and continuously monitoring and improving your case-picking operations can further optimize labor utilization and mitigate the impact of labor shortages.
Preventive Maintenance:
Implementing a preventive maintenance schedule helps identify and address potential issues before they lead to breakdowns. Lexicon Tech Solutions can conduct routine checks, lubrication, adjustments, and replacements as needed to keep equipment in optimal condition and avoid downtime.
Batch Picking:
Group similar orders together so that a single picker can pick items for multiple orders in one trip through the warehouse. This reduces travel time and increases efficiency.
Zone Picking:
Divide the warehouse into zones and assign pickers to specific zones. Each picker is responsible for picking items within their designated zone, reducing congestion and minimizing travel time.
Strategies to Enhance Accuracy and Customer Satisfaction
In case picking, getting it right is crucial. A tiny mistake can cause wrong shipments, unhappy customers, and even lost business. To keep things accurate and make customers happy, try these strategies:
Comprehensive Staff Training:
Accuracy starts with well-trained and knowledgeable staff. Provide comprehensive training programs that focus on the correct picking methods, attention to detail, and proper use of technology tools such as barcode scanners. Implement quality control measures to double-check picked items before packing, reducing the chances of errors slipping through. Regularly review and address any process bottlenecks or common errors to continuously improve the accuracy of your case-picking operations.
Effective Order Fulfillment Processes:
Efficient order fulfillment processes are essential for accurate case picking. Implement clear and well-structured workflows that minimize confusion and ensure every step is followed systematically. Assign designated picking zones and utilize effective zone-picking techniques to prevent cross-contamination or mix-ups. Incorporate technology solutions like automated order-picking software to guide employees through the picking process, reducing the chances of errors and enhancing efficiency.
Precise Inventory Management:
Accurate inventory management is a critical component of successful case picking. Maintain a real-time inventory tracking system or utilize warehouse management software to ensure accurate stock levels and improve visibility. Regularly conduct cycle counts and reconcile inventory to identify any discrepancies and rectify them promptly. A well-maintained and organized warehouse with accurate inventory data minimizes picking errors and streamlines case-picking operations.
Single Order and Single Pallet Picking:
While case picking may involve picking full cases, it’s crucial to maintain accuracy even for individual orders or single pallets. Implement robust picking processes, such as discrete order picking, where individual items are picked from different locations. Utilize technology tools like barcode scanners to ensure correct item selection and accurate fulfillment. By focusing on accuracy at all levels, you can meet the diverse needs of your customers and maintain their satisfaction.
Optimize Your Warehouse Operations with Lexicon Tech Solutions
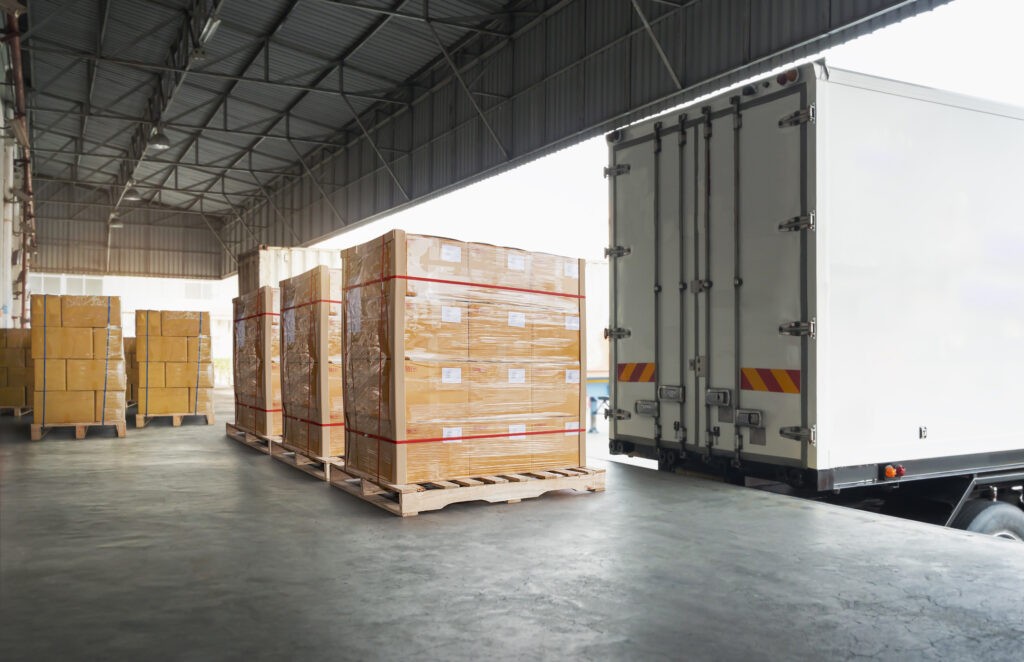
Lexicon Tech Solutions can play a pivotal role in streamlining and optimizing warehouse operations, through a range of comprehensive maintenance services and solutions:
- Preventive Maintenance Expertise: Lexicon Tech specializes in preventative maintenance for warehouse equipment and technology. By regularly inspecting, servicing, and fine-tuning case picking machinery, they ensure optimal performance, minimizing downtime due to unexpected breakdowns.
- Customized Maintenance Plans: Lexicon Tech tailors maintenance plans to the unique needs of your warehouse, considering the type of equipment used, the volume of orders, and other operational factors. This proactive approach prevents disruptions and extends the lifespan of your equipment.
Ready to elevate your warehouse operations to the next level of efficiency? Contact Lexicon Tech Solutions today to unlock the power of proactive maintenance. Our expert team is here to optimize your equipment’s performance, minimize downtime, and maximize your operational success.